DataMesh Director New Version Released! Major Upgrades to Training Mode
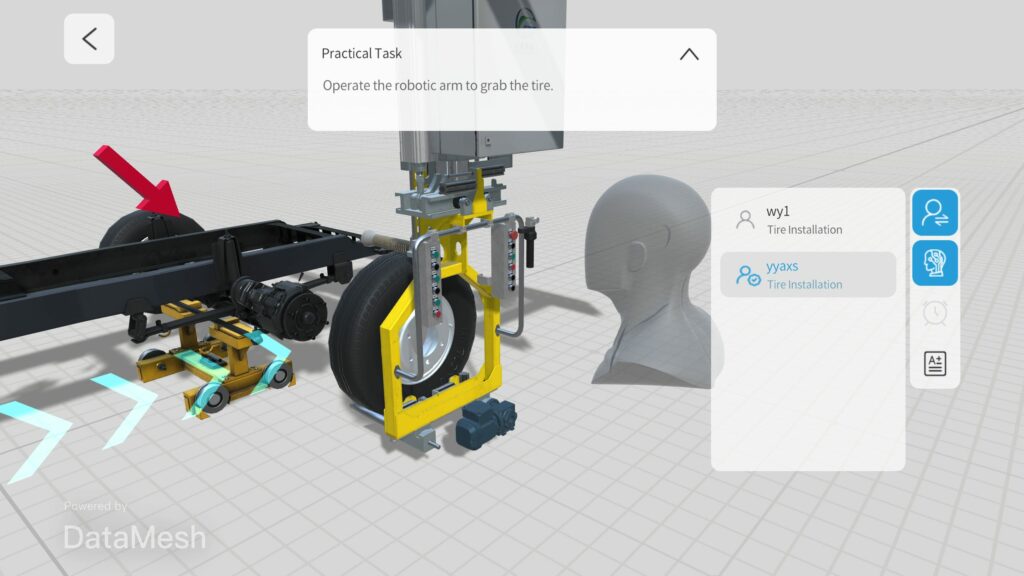
The latest version streamlines the courseware creation process with templated question formats, introduces a new Key Question mechanism to enhance risk management in high-risk industrial training scenarios, along with an invigilation feature that enables real-time monitoring of student performance.
DataMesh FactVerse Supports Foxconn to Enhance Employee Training and Equipment Maintenance Efficiency
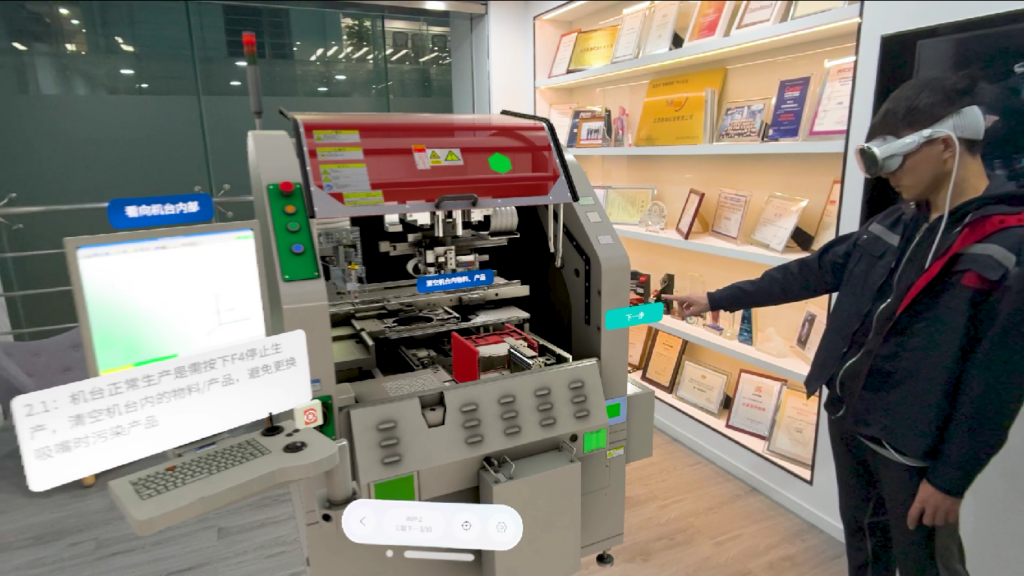
With the support of DataMesh FactVerse platform and Apple Vision Pro, Foxconn enables its frontline employees to easily create mixed-reality training materials and inspection plans, and complete training and inspection tasks in a simpler and more intuitive way, resulting in significant improvements in work performance.
DataMesh Director Gets a Major Upgrade: The New “Storyline”
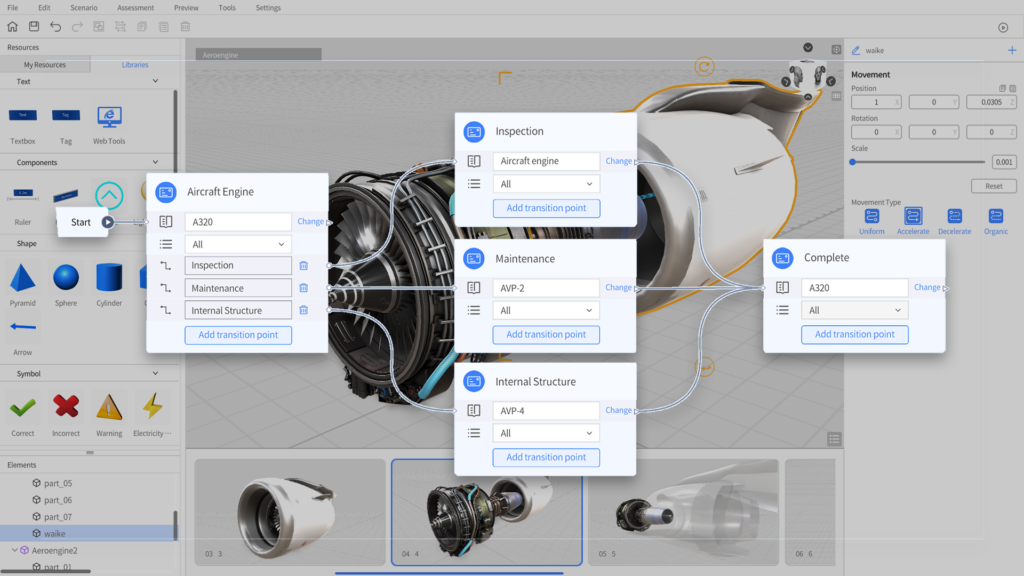
The latest version of DataMesh Director introduces the new trial feature “Storyline”, which is especially useful for managing scenarios for large exhibition projects and complex operational guidance. Additionally, the new version also brings optimizations in model preprocessing and viewer experience.
Collaboration Between JTC & DataMesh: Advancing Construction Efficiency with Digital Twin and Mixed Reality
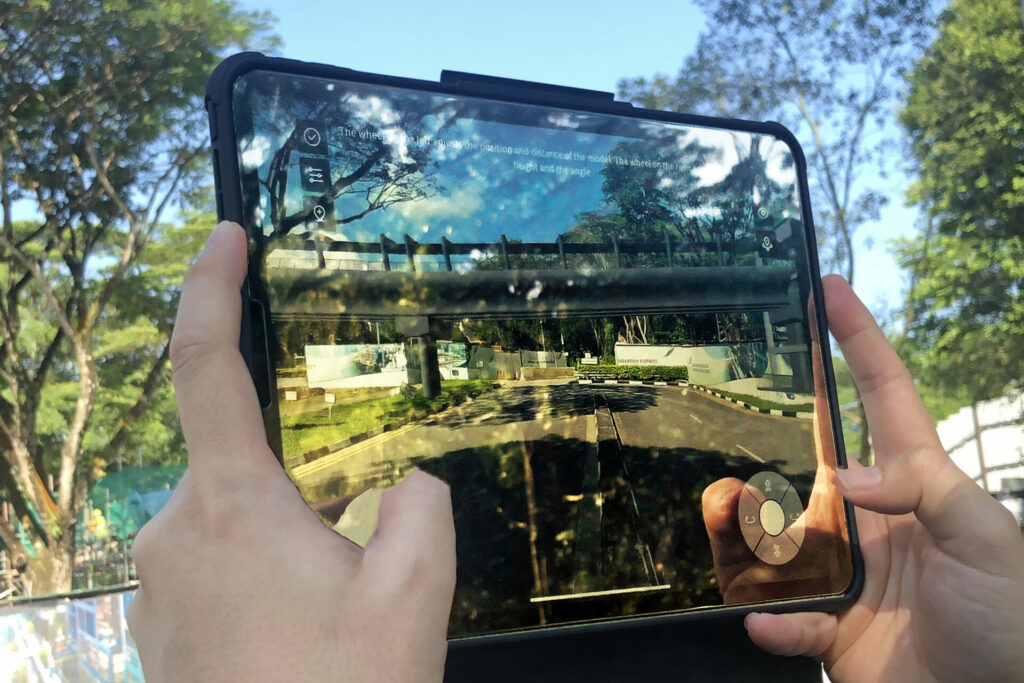
By integrating BIM data with MR technology, the platform empowers frontline workers to visualise and understand complex construction tasks in both virtual and real-world spaces, significantly improving efficiency on job sites.
Accelerating Industrial Metaverse: FactVerse Updates August 2024
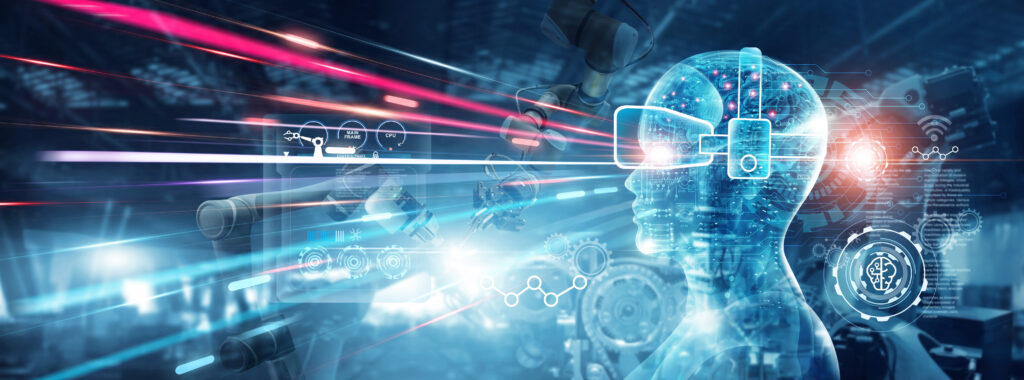
FactVerse platform introduces valuable enhancements and optimizes performance for frontline business scenarios to help enterprises integrate digital twin technology into their operations more efficiently, driving progress toward intelligent manufacturing, smart maintenance, and sustainable development.
Inspector 1.2 Released: Uncover Hidden Building and Facility Information for Smart Management with Mixed Reality
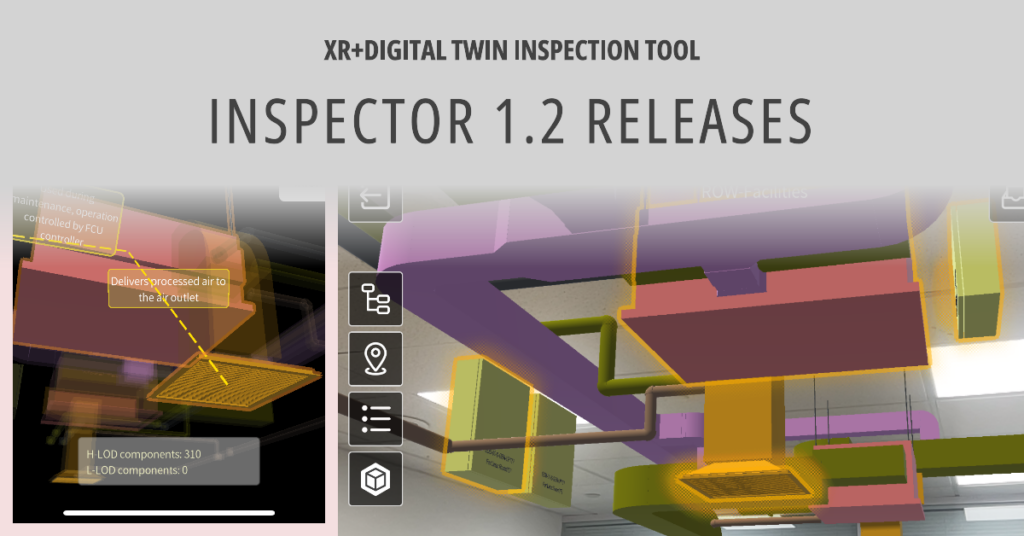
Quickly generate digital twin scenes, dynamically load BIM data on the go, and effortlessly inspect hidden details behind devices and equipment. With DataMesh Inspector 1.2, managing and maintaining buildings has never been easier.
DataMesh FactVerse Updates Released for Industrial Digital Twin Innovation

Enhancements across the entire FactVerse ecosystem to support enterprise users in constructing digital twin scenarios, fostering symbiotic virtual and real environments, and seamlessly integrating with business applications.
DataMesh Contributes to Success of SMART MANUFACTURING SUMMIT
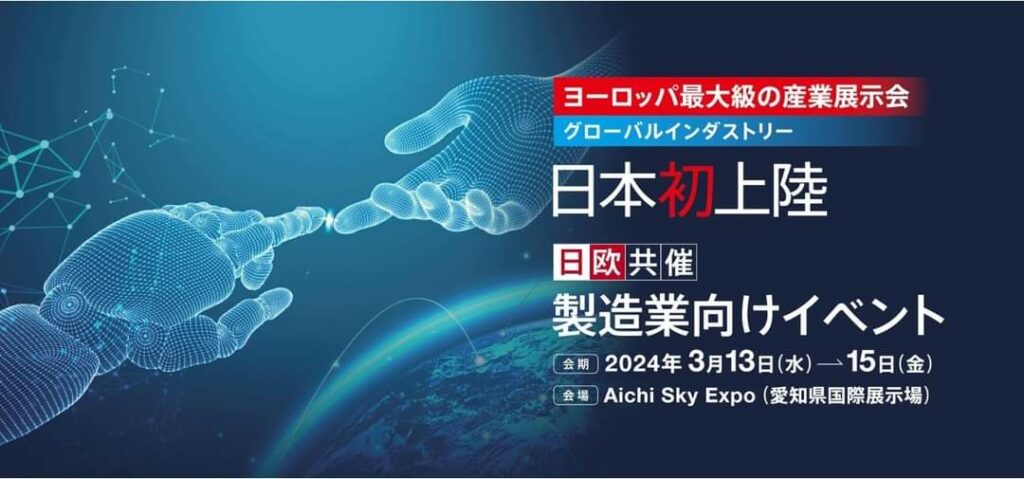
Collaborating with Aichi Prefecture Government and KDDI, DataMesh contributes to the summit by creating an immersive digital industrial landscape based on MR technology, enhancing the attendee experience for the SUMMIT driving Industry 5.0 and innovation between Japan and Europe.
FactVerse Express Opens for Global Creators to Innovate in XR Amid Spatial Computing Trend
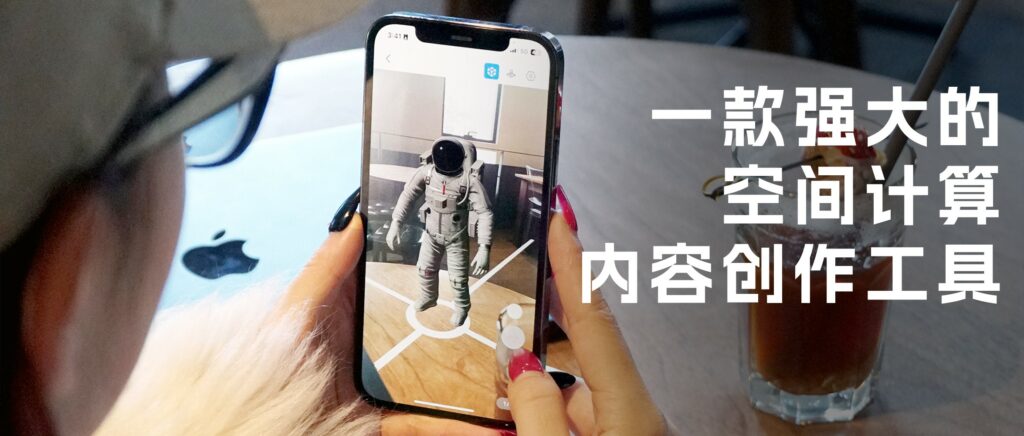
FactVerse Express is compatible with Apple Vision Pro, ready to empower users across platforms with an exceptional spatial computing experience upon the availability of Apple Vision Pro, in addition to its existing support for various devices, including Meta Quest 3, iPhone, and iPad.
DataMesh Reshapes Tower Crane Training Experience with Simulator 2.1
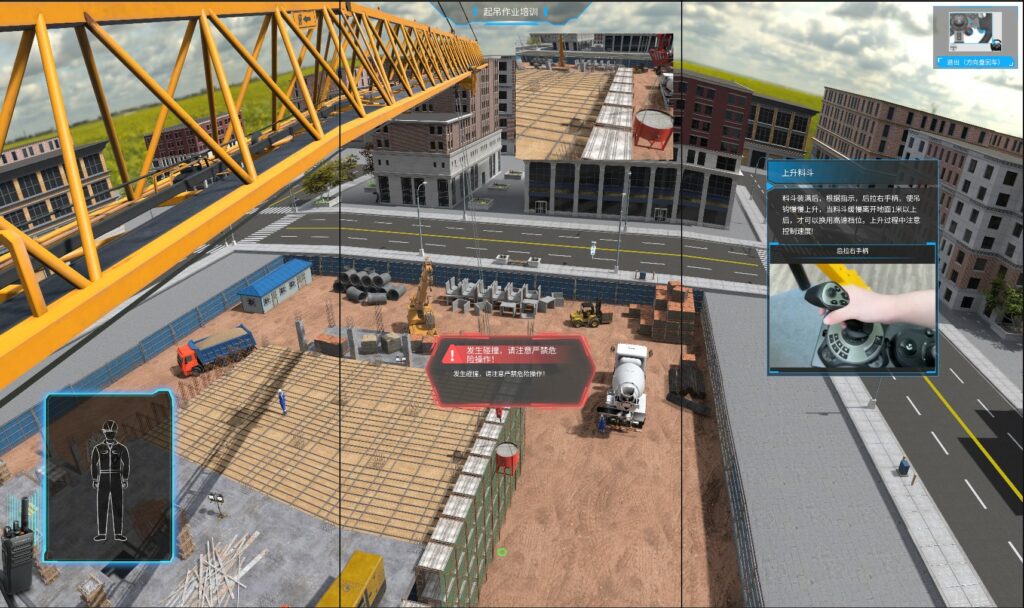
Simulator 2.1 introduces brand-new simulation-based training and assessment experience tailored for tower crane operations, through upgraded operational scenarios that faithfully replicate real equipment models, construction environments, and operational procedures.