DataMesh FactVerse Powers NIO’s Smart Factory Transformation with Digital Twins
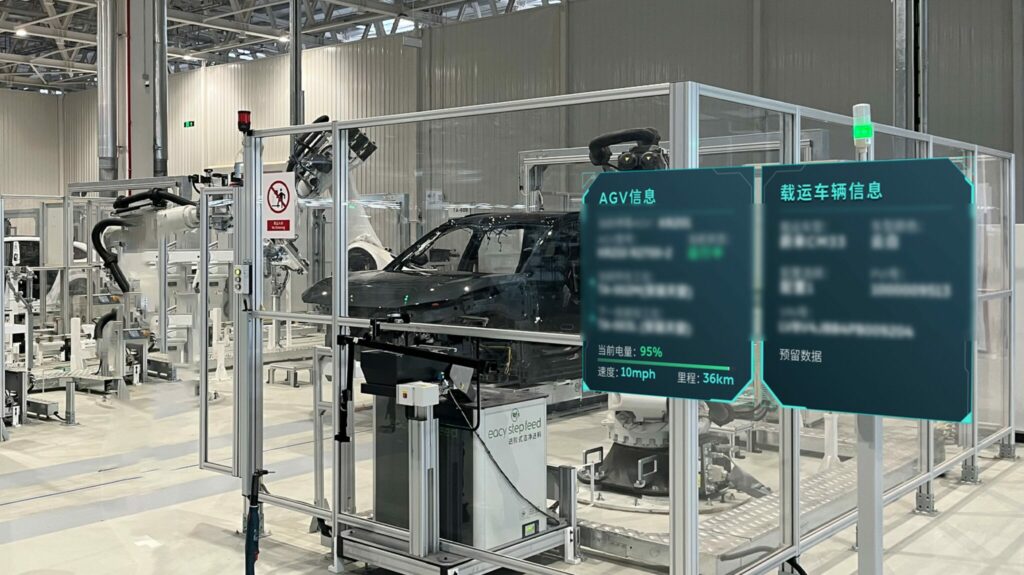
In collaboration with DataMesh, NIO deployed a Production Management Center (PMC) digital twin platform for its vehicle assembly line. Powered by FactVerse, this platform transforms production management by enabling comprehensive simulation and real-time monitoring of the entire production process within a highly detailed 1:1 digital twin factory.
DataMesh FactVerse Supports Foxconn to Enhance Employee Training and Equipment Maintenance Efficiency
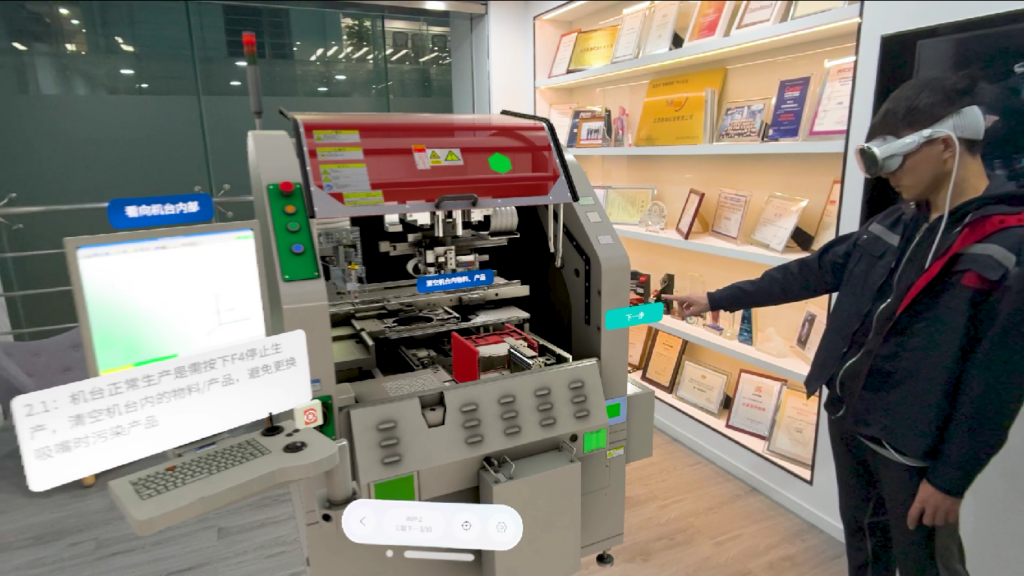
With the support of DataMesh FactVerse platform and Apple Vision Pro, Foxconn enables its frontline employees to easily create mixed-reality training materials and inspection plans, and complete training and inspection tasks in a simpler and more intuitive way, resulting in significant improvements in work performance.
Collaboration Between JTC & DataMesh: Advancing Construction Efficiency with Digital Twin and Mixed Reality
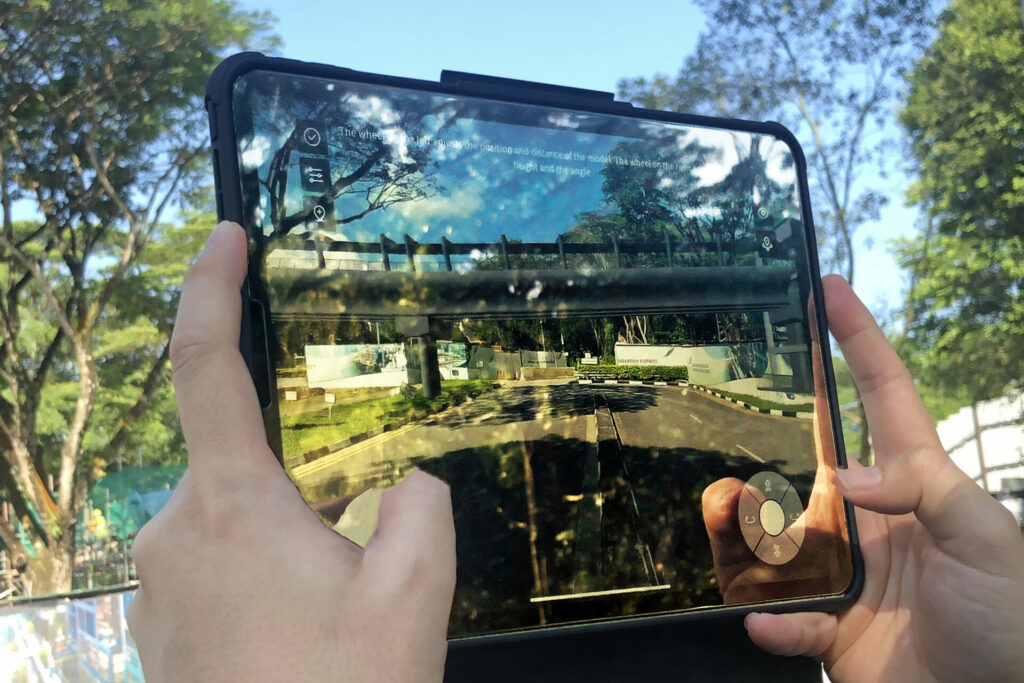
By integrating BIM data with MR technology, the platform empowers frontline workers to visualise and understand complex construction tasks in both virtual and real-world spaces, significantly improving efficiency on job sites.
Digital Twin + XR Projection Tour of “TOKYO TORCH/Torch Tower” Successfully Concluded
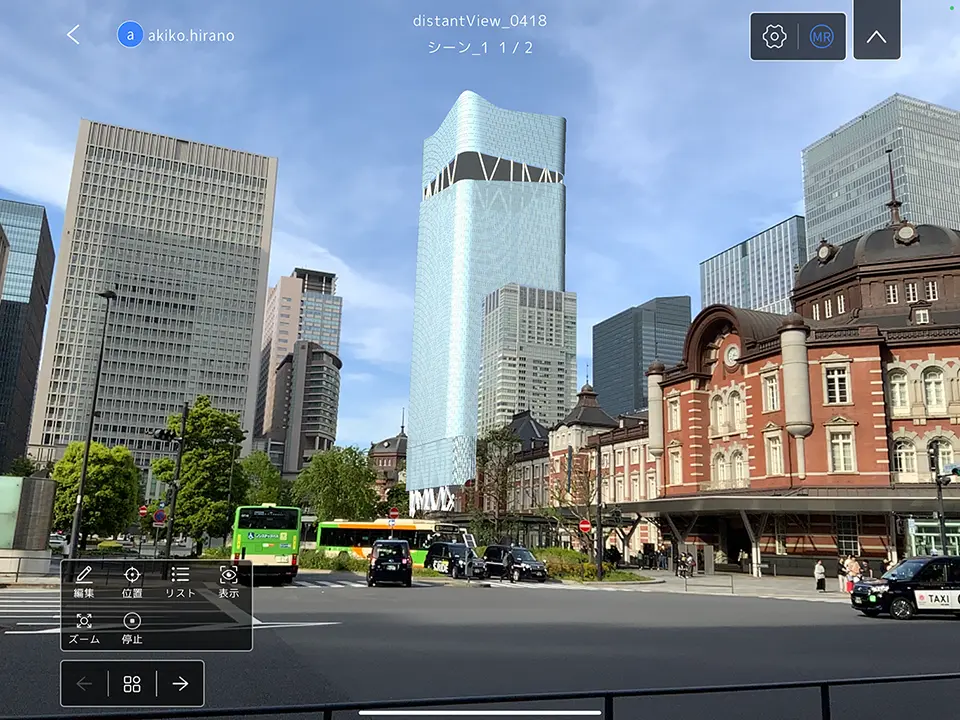
Aimed at verifying the visualization effects of the planned building through the use of Digital Twin and XR, the event held at the planned site of the “Torch Tower,” has received positive feedback from various stakeholders.
DataMesh Transforms Maintenance Processes for Swire Coca-Cola with 100+ Accelerator
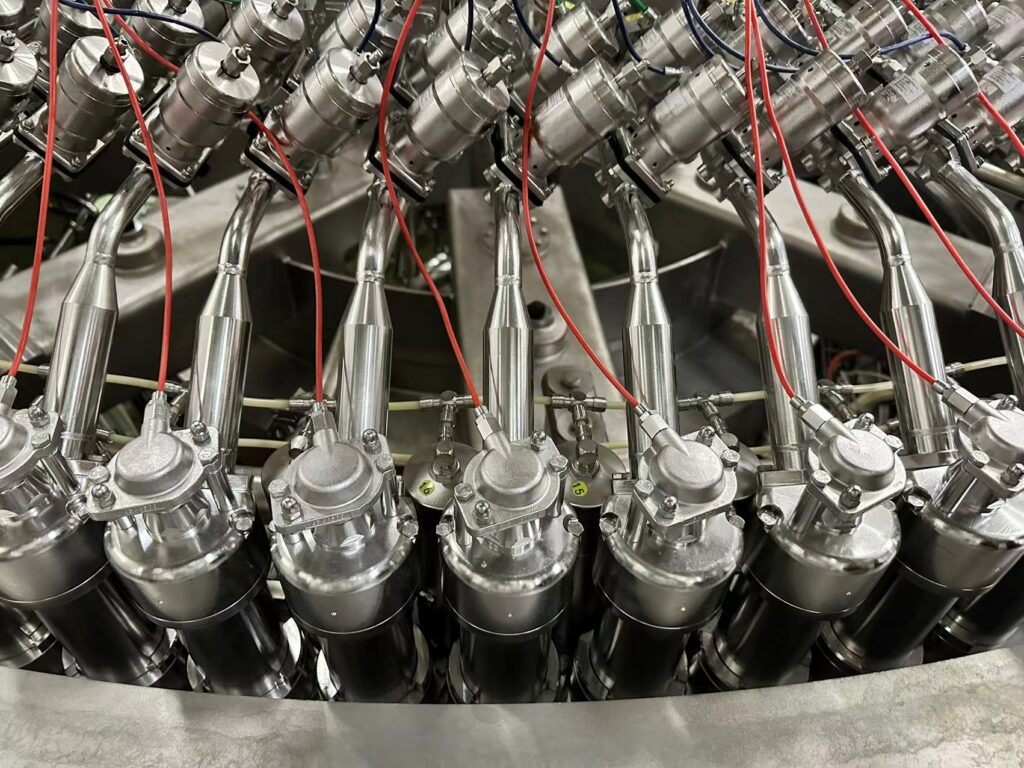
With DataMesh’s digital twin and MR technology, frontline workers now perform complex maintenance tasks more efficiently, reducing downtime and operational costs while creating new job opportunities.
An education and training tool utilizing MR and Digital Twins to improve engineer skills to ensure expressway safety
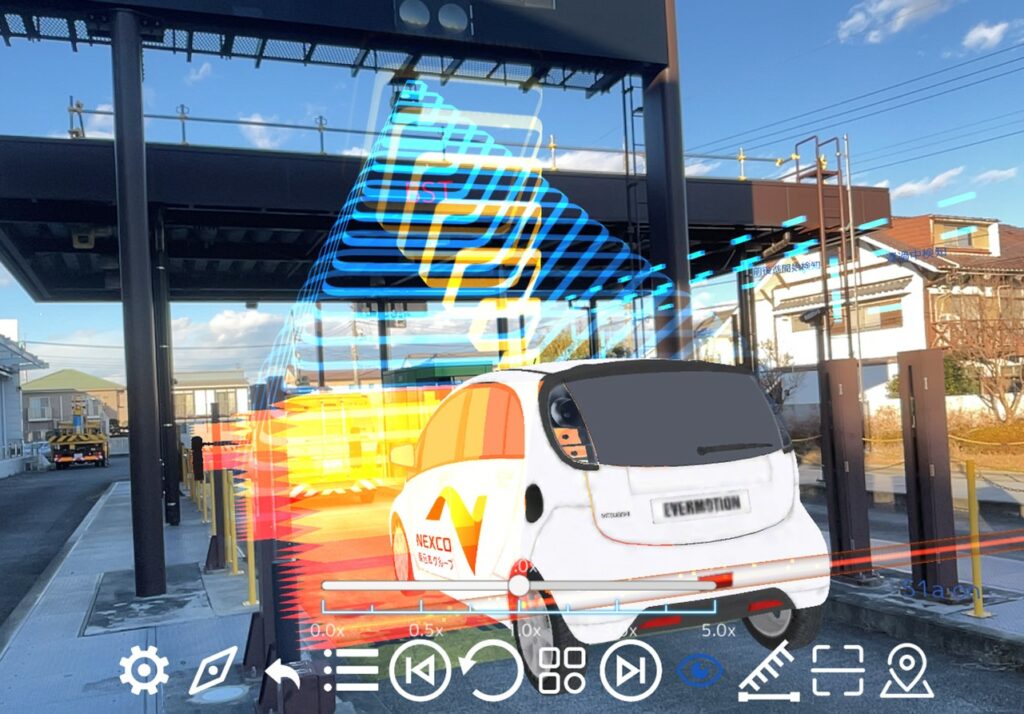
Supporting Nexco-East Engineering in developing a cutting-edge training app to address the challenges of the vast expressway network, achieving efficient training and ensuring engineers can excel in their roles with the needed expertise.